BEMO-COFRA is developing a software platform for monitoring and control of large-scale production systems which can meet the market demands for flexible and holistic production in the manufacturing industries
- There is an increasing need for flexibility in production activities that can adapt to a continuously changing world market. The manufacturing industries require processes that are more flexible and that can better adapt to shifting consumption patterns. The key issue to survive in a worldwide competition will be the capacity of putting new and innovative products on the market and enhancing system flexibility through advanced ICT tools and architectures, explains Eduardo Souto, Associate Professor at the Institute of Computing of the Federal University of Amazonas.
- In this context, BEMO-COFRA is developing an innovative distributed framework which allows networked monitoring and control of large-scale complex systems by integrating heterogeneous smart objects, legacy devices and sub-systems, cooperating to support holistic management and to achieve overall systems’ efficiency with respect to energy and raw materials, Eduardo Souto continues. Today, manufacturing systems often suffer from a lack of flexibility and integration. There is limited integration between the processes involved in the engineering and management of the plants; difficulties in providing flexibility in the production plant to accommodate for continuously varying product mixes and volumes as well as a lack of scalability, reconfigurability and manufacturing efficiency. - Addressing these main weaknesses through the creation of specific scenarios and requirements, makes it possible for us to provide generic solutions which can help resolve the weaknesses and thereby enhance overall efficiency and strengthen the competitiveness, Eduardo Souto explains.
Complex management made easier online
To integrate, monitor and control the many devices and sub-systems in a complex production environment, the BEMO-COFRA framework provides a middleware which is able to expose the capabilities of smart objects, legacy devices and sub-systems and transform them into web services. Syntactic and semantic interoperability is made available among coexisting technologies in the overall monitoring and control framework. WSAN (Wireless Sensors and Actor Networks) devices, legacy sub-systems and other devices will thus be able to interact and cooperate, orchestrated by a manager in charge of enforcing a distributed logic with the overall monitoring and control network.
To support the adoption of large-scale networks composed of heterogeneous smart objects with sensing and actuating capabilities, devices are integrated through heterogeneous wireless communication technologies such as WiFi, BlueTooth or IEEE 802.15.4-based technologies.
- The WSANs to be developed by BEMO-COFRA will also feature the flexibility, reliability, availability and manageability characteristics that are of paramount importance to support dependable operations in harsh environments, Eduardo Souto explains.
The achievements are demonstrated by deploying the BEMO-COFRA framework in a car manufacturing plant provided by partner COMAU and the FIAT Group where dependability of the system is of utmost importance and where a very large number of devices, systems and WSAN devices interact and actively cooperate with each other to enable a very accurate observation of production processes.
In the next sections, Eduardo Souto explains the basic vision of BEMO-COFRA and its functionality.
Vision and conceptual approach
The BEMO-COFRA framework addresses both technological aspects and user needs to promote a software platform for monitoring and control which is able to provide:
1. Integration of legacy devices, systems and different wireless heterogeneous technologies into an overall framework, and turn them into useful, value-added business services or service components.
2. Novel mechanisms to enforce dependability in WSANs operating in harsh environments and serving heterogeneous application constraints by means of context awareness, self-configuration and self-adaption capabilities.
3. Adopting distributed and decentralised approaches to provide WSANs with scalable monitoring, control and self-diagnosis capabilities.
4. Introducing a Service Oriented Architecture (SOA) and a middleware that, by exposing smart objects capabilities as web services, make it possible for the innovative WSAN to be developed within the project to cooperate with legacy devices and systems.
The above BEMO-COFRA achievements clearly pave the way to an innovative framework supporting networked monitoring and control systems in different application domains, as shown in the figure below.
The overall BEMO-COFRA system represents a comprehensive, distributive framework comprising a middleware layer, large WSANs, PLC and SCADA systems, and not least computers and powerful devices being deployed in manufacturing plants.
The BEMO-COFRA architecture The BEMO-COFRA platform is proposed as service-oriented, consisting of five loosely coupled core layers and their respective components. Each of the layers and their components presented in the figure below are responsible for their respective part of the overall functionality.
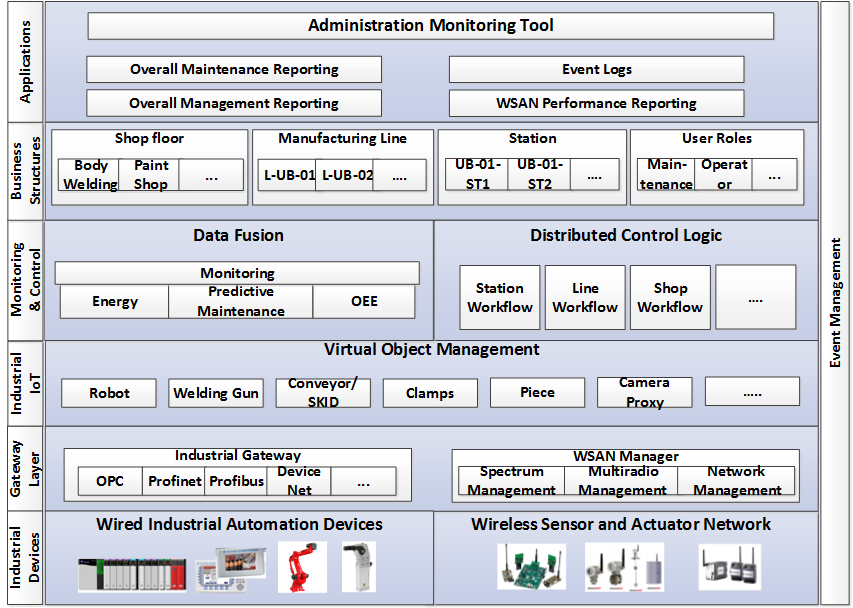
Applications
The BEMO-COFRA application components encompass administration, monitoring and configuration tools and also all user interfaces designed to provide access and generate information based on the environmental data. The application layer includes the tools offered, including:
1. Generation of Overall Maintenance Reporting – This application offers support to the preventive maintenance activities with indications of which resources will soon need attention or reach their final life cycle.
2. Access Event Log – This interface allows the access to system events available in the BEMO-COFRA environment and generated by all integrated resources.
3. Generation of WSAN Performance Reporting – This unit generates status reports from all WSAN monitored devices for control and evaluation proposes. It is a helpful tool for the system administrators.
4. Business Intelligence Management – This application transforms raw data into meaningful and useful information for business purposes to help identify and develop new opportunities. It supports the implementation of an effective strategy thereby being able to provide a competitive market advantage and long-term stability, offering historical, current and predictive views of business operations.
Core services
The BEMO-COFRA architecture provides a set of core services used to compose the information required by application domains. This composition is done by a service layer which interacts with the application layer to communicate with user-developed applications that want to access and use the services offered in this layer. The following types of components are found in the service layer:
1. Data fusion component. Data fusion is an important component of applications for systems that use correlated data from multiple sources (sensor and other device readings) to determine the state of a system. As the state of the monitored system can change, the general data fusion component should change dynamically based on the current environment and available resources in the system. To achieve this goal, the Data Fusion Component analyses data provided by the lower layers, including industrial IoT and the business structure layer and provides an overview of the manufacturing plant through the semantically enriched monitoring reports.
2. Distributed Control Logic component. The BEMO-COFRA architecture defines a Distributed Control Logic component aimed at effectively orchestrating the application-oriented monitoring and control services operated within the overall system. The services provided by this component enable monitoring and control of the overall networked community of cooperating objects composed by WSANs and different sub-systems. The control logic monitors the devices distributed on the line and controls them, indicating their correct time to act or not. The control logic system proposed is composed by sensors, actuators and PLCs (Programmable Logic Controllers), which control the other devices. The flow of the production is mapped regarding the correct station sequence, order of activities, devices activation and status and then the logic is inserted on the PLC. Features as alarms and line stop must be predicted for the control logic, which is based on the Poka-Yoke methodology.
3. Virtual Object Manager. The Virtual Object Manager component provides virtual objects for the Data Fusion and Distributed Control Logic components. The virtual objects are logical devices built from resources of the wired industrial automation devices and wireless sensor and actuator networks present in the manufacturing plant, e.g., a welding robot with wireless power consumption sensor could be represented by a virtual object by the name ‘energy-aware welding robot’.
Virtual entities
A manufacturing scenario can be identified with that of a generic user that needs to interact with (possibly remote) physical entities such as robots, PLCs, clamps, skids, and so on. In this scenario, people (e.g., operator and maintenance crews) or some artifact (e.g., a service or application) that have an interest in interacting with a physical entity can do it through the virtual entities in the BEMO-COFRA architecture.
When the interactions occur directly, e.g., by moving a robot from A to B manually, the BEMO-COFRA architecture allows a mapping between physical and virtual entities, providing the user a better capacity interaction with the physical environment. From the Virtualization Layer, the user is able to interact indirectly or mediated, i.e., by calling a service that will either give information about the physical entity or actuate it. The virtual entities are representations of a set of properties and parameters of the physical entity. This means that changes that affect the virtual entity could manifest themselves in the physical entity.
Industrial gateways
The industrial gateway component is responsible for exposing functionality from wired industrial automation devices. This includes everything from simple sensors to more advanced devices such as PLCs and robot controllers. The following figure depicts a functional view of the industrial gateway layer, including a device application catalogue, discover managers and IoTDevices. Each of the components is described in detail below:
1. IoTDevice - An IoTDevice is a combination of a Device Service Manager and Device Services created by the Discovery Manager. The IoTDevice is the interface that is shown to the rest of the system to interact with the devices. In addition to this, the IoTDevice has local storage that can be used to log sensor readings over a long time.
2. Device Service Manager - The Device Service Manager acts as the driver for communicating with devices using a certain protocol. For each protocol that is used a specific Device Service Manager manages the communication.
3. Device Services - The Device Services component provides the interface to the device with both properties and methods. For each device type there needs to be a specific Device Service component. For instance, a thermometer device can implement the property currentTemperature. Devices that are more complex can include more sophisticated methods in their Device Services.
4. Device Application Catalogue - The Device Application Catalogue component provides a catalogue of all known IoTdevices in the Industrial Gateway. This is the service that provides a mechanism for searching for different IoTdevices in the gateway. It also contains meta-information with regards to the IoTdevices such as device type, services offered, status etc.
Industrial devices
The industrial device component is responsible for direct interaction between all components existing in an electronics factory floor and should be controlled by the architecture. The component "Wired Industrial Automation Devices" is responsible for tracking events of devices and send information such as the upper layers Gateway Layer. Importantly, this layer is responsible only for devices with a wired interface whereas wireless interface devices are controlled by the component "Wireless sensor and actuator network". This component will be responsible too for the storage and management of the device drivers.
In the factory floor, a multitude of devices and components that compose the factory scenario are found.
Related deliverable: D3.1 Robotics and Sensor Integration
to
the top 
|